O-Ring Sizing Tools
Get free shipping on qualified O-Ring products or Buy Online Pick Up in Store today. The Installation Tool consists of a collar made from an impact resistant material which is profiled to suit a particular seal. The tool 'clips' over the seal face, protecting the lapped surface and resting on the O-ring (Fig. Installation Tools are designed to locate on the O-ring so that as force is applied.
• O-Ring sizing cones and measuring tools
To install an O-Ring energized piston seal into a closed groove with tools, first insert the O-Ring into the piston-seal groove using the method described above. Then place an installation cone over the piston and align it with the seal groove.
O-Ring Sizing Tools Available to Order Online:
Quick reference devices to help confirm most common USA standard o-ring sizes Mobo robo. Kakao emoji.
Quick reference tape measure confirms metric size O-Rings 64mm-665mm Inside diameter on one side and USA AS568 standard O-Ring sizes from 2.5'ID to 26' inside diameter on the other side. Metric and Inch Cross Section thickness reference gauge. (Consider a Sizing Cone for small O-Rings under 2.5' inside diameter.)
The ORID will help distinguish between Viton®, Kalrez®,
Nitrile and EPDM o-ring materials of 100, 200, 300 and 400 series
O-rings 60 to 80 Durometer.
Quick reference device to help indicate common USA standard o-ring sizes 1/4' thru 5-5/8' ID, in five standard USA cross-sections.
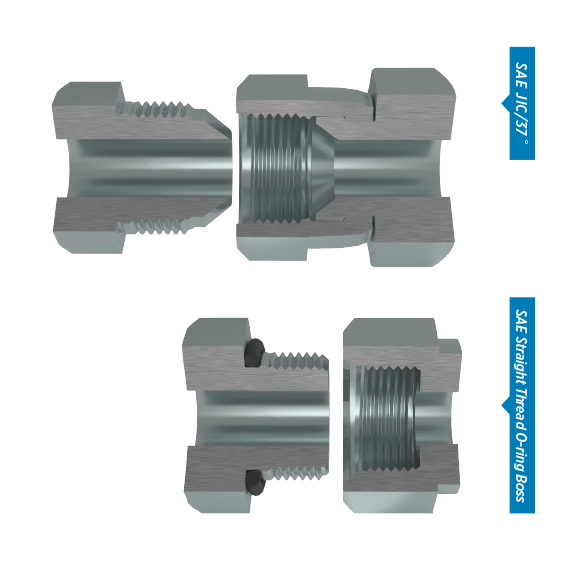
Quick reference device to help confirm common USA standard o-ring sizes (color and branding may vary)
Article re-posted with permission from Parker Hannifin Sealing & Shielding Team.
Original content can be found on Parker's Blog.
Incorrect O-ring installation can lead to assembly damage causing leakage during the first pressure test. If the system does not pressurize properly, the entire piece of equipment should be disassembled and seals must be replaced. Depending on when this test occurs, multiple manufacturing steps could be in between the seal installation and the first step where leakage can be identified. If O-ring damage happens with high frequency, you could be wasting time and money on seal replacement. Luckily, there are some easy steps that can be followed to help prevent this from occurring. Parker's recommended guidelines for installation include always using lubrication, good gland design, and ensuring correct sizing.
Lubrication Makes Installation Easier
Using lubrication is an essential facet of proper installation. Lubrication reduces surface friction between the O-ring and mating surfaces, allowing the O-ring to seat in the groove with very little difficulty. Ilivid apps. In male and female radial seals, lubrication will reduce installation force and create a smooth transition as the piston is inserted in the bore.
Choosing the proper lubricant requires careful consideration of your system. You must ensure the lubricant choice is compatible with the material being used, suitable for the temperature range of the application, compatible with the system fluids, capable of producing a high surface tension film, and does not clog system filters.
Parker offers two lubricants, O-Lube and Super-O-Lube. The O-Lube is an outstanding general-purpose grease intended for O-ring and elastomer seal types used in hydrocarbon service. O-Lube has a recommended service temperature of -20°F to 180°F (-29°C to 82°C). On the other hand, Super-O-Lube is an ideal all-purpose O-ring lubricant. Rather than a grease, the Super-O-Lube is a high viscosity silicone oil. It is an extremely effective seal lubricant, useful from -65°F to 400°F (-54°C to 204°C).
For more information on Parker O-Lube and Super-O-Lube and how to choose a lubricant, refer to section 3 of the O-Ring Handbook.
Good Design Principles
One of the easiest ways to ensure care-free installation is by following good design practice as recommended in the Parker O-Ring Handbook. The dimensions listed in the O-Ring Handbook put good compression on the O-ring while preventing the groove from exceeding 100% fill. In radial seal applications Parker recommends using a lead in chamfer at an angle of 15-20 degrees with an opening which exceeds the maximum height of the O-ring in the groove.

Quick reference device to help confirm common USA standard o-ring sizes (color and branding may vary)
Article re-posted with permission from Parker Hannifin Sealing & Shielding Team.
Original content can be found on Parker's Blog.
Incorrect O-ring installation can lead to assembly damage causing leakage during the first pressure test. If the system does not pressurize properly, the entire piece of equipment should be disassembled and seals must be replaced. Depending on when this test occurs, multiple manufacturing steps could be in between the seal installation and the first step where leakage can be identified. If O-ring damage happens with high frequency, you could be wasting time and money on seal replacement. Luckily, there are some easy steps that can be followed to help prevent this from occurring. Parker's recommended guidelines for installation include always using lubrication, good gland design, and ensuring correct sizing.
Lubrication Makes Installation Easier
Using lubrication is an essential facet of proper installation. Lubrication reduces surface friction between the O-ring and mating surfaces, allowing the O-ring to seat in the groove with very little difficulty. Ilivid apps. In male and female radial seals, lubrication will reduce installation force and create a smooth transition as the piston is inserted in the bore.
Choosing the proper lubricant requires careful consideration of your system. You must ensure the lubricant choice is compatible with the material being used, suitable for the temperature range of the application, compatible with the system fluids, capable of producing a high surface tension film, and does not clog system filters.
Parker offers two lubricants, O-Lube and Super-O-Lube. The O-Lube is an outstanding general-purpose grease intended for O-ring and elastomer seal types used in hydrocarbon service. O-Lube has a recommended service temperature of -20°F to 180°F (-29°C to 82°C). On the other hand, Super-O-Lube is an ideal all-purpose O-ring lubricant. Rather than a grease, the Super-O-Lube is a high viscosity silicone oil. It is an extremely effective seal lubricant, useful from -65°F to 400°F (-54°C to 204°C).
For more information on Parker O-Lube and Super-O-Lube and how to choose a lubricant, refer to section 3 of the O-Ring Handbook.
Good Design Principles
One of the easiest ways to ensure care-free installation is by following good design practice as recommended in the Parker O-Ring Handbook. The dimensions listed in the O-Ring Handbook put good compression on the O-ring while preventing the groove from exceeding 100% fill. In radial seal applications Parker recommends using a lead in chamfer at an angle of 15-20 degrees with an opening which exceeds the maximum height of the O-ring in the groove.
O Ring Installation Tapered Cone Setup
Want to know more about installation of specific groove types? Parker has produced easy to follow videos showing how to install O-rings in dovetail grooves, face seals, and male and female radial seals.
Proper Sizing is Key
Putting the wrong sized O-ring into an application can also lead to damage, making it important to verify sizing to ensure the right O-ring was selected. Unfortunately, measuring O-rings in the field or in a warehouse is not easily done without the proper tools. Parker offers a unique solution to this problem by offering measuring cones and circumference 'Pi' tape to help provide quick and easy sizing information. These tools will help ensure that the proper Parker standard size is chosen during assembly.
O Ring Installation Tapered Cone Settings
Applications Help for Further Assistance
Tapered Cone Collar
By following the above recommendations you can be at ease during manufacturing your product. If you do encounter issues during your assembly that fall outside our recommendations, Parker can help troubleshoot your situation. Parker O-Ring Division application engineers can assist with your particular application. Our engineers can be reached a variety of ways, via telephone, email, and even online chat. With this additional help you can be sure that you will find success using Parker O-Rings.
This article was contributed by Eric Uehlein, Applications Engineer, Parker O-Ring Division.
Source: http://blog.parker.com/3-guidelines-to-ensure-proper-seal-installation